High-quality conveyor rollers and idlers for belt conveyors - the most important quality features
How do you recognize the quality of a conveyor roller for belt conveyors in bulk material handling? High-quality conveyor rollers can be recognized by certain features. The most important feature is always their long, trouble-free service life. Good conveyor rollers must always have the lowest possible running resistance, good concentricity and imbalance properties as well as low noise emissions.
As this is not a new topic, most of the parameters and the corresponding test methods are already established and standardized. The most important standards for this topic in Germany are DIN 22112 and DIN 15207.
We have summarized the most important parameters for you in a table.
Parameters | Target values |
Dimensional accuracy | Acc. to DIN 22112 and DIN 15207 |
Axial displaceability (axial play) | Acc. to DIN 22112-2. |
Bearing clearance and tolerance class of the bearings | For deep groove ball bearings: C4 and P0 acc. to DIN 22112-2 |
Cage | For deep groove ball bearings: plastic cage acc. to DIN 22112-2 |
Bearing seat fits | Acc. to DIN 22112-2 |
Bearing seals | We use Z-shields on both sides. |
Push-out resistance | >12kN (acc. to DIN 22112-2) |
Runout | Max. permissible tolerances acc. to DIN 22112-2. The strictest requirement is the equivalent of 0.8mm/m. |
Tightness | Our seals surpass the requirements of DIN 22112-3 and all other standards. |
Lubrication | 50 - 60% of the free bearing volume must be filled with lithium-saponified grease. |
Running resistance (running friction force) - during start-up and operation | It should be as low as possible, as it has a direct influence on wear of the idler rollers and the belt as well as on the energy consumption of the conveyor. For bearings up to 6306, see DIN 22112-2. It depends on the diameter of the roller and the bearing size. A value of 10N must not be exceeded under any circumstances. |
Balancing quality | Depending on the design, our conveyor rollers have balancing quality classes acc. to ISO 1940 of at least ≤G40 at belt speeds of up to 3m/s to ≤G14 at belt speeds of up to 10m/s. |
Compliance with the max. permissible bearing misalignment* | Under full load, the bearing misalignment for deep groove ball bearings should not exceed 10 arc minutes (see DIN 22112-2). For spherical roller bearings, up to 2° is permissible. |
Calculated bearing service life* | We recommend L10 > 60,000h. |
Noise emissions | If relevant, the maximum sound power level of the conveyor rollers must also be taken into account (see "TA Lärm"). With our noise-reduced conveyor rollers, we achieve a reduction in the sound power level of approx. 20 dB(A). |
* Calculated verification of suitability for operation in the specific conveyors.
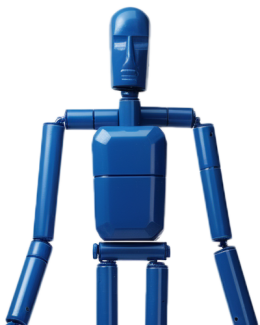
Your contact person
-
Idlers sales
-
+49 (2041) 177 - 227
-
Idlers and conveyor belt rollers
-
+49 (2041) 177 - 0